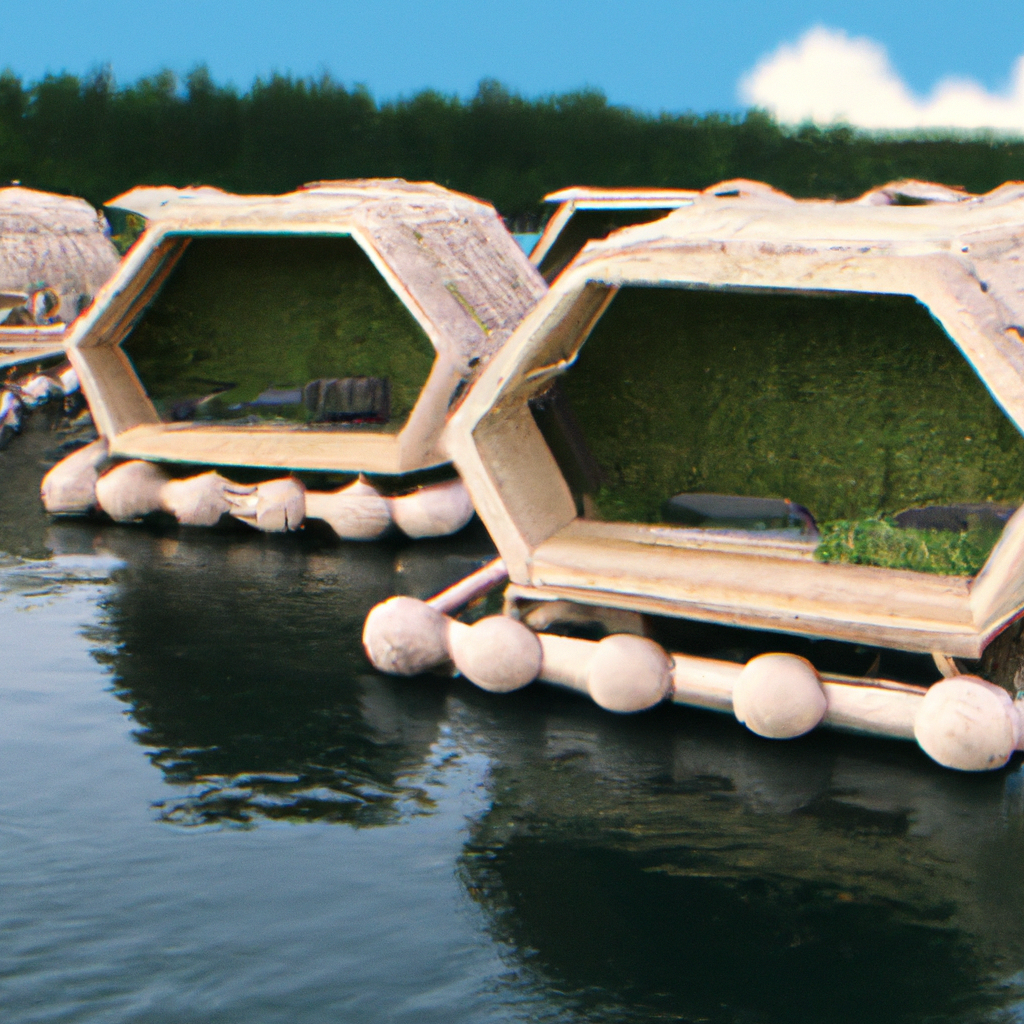
Hemp as a Sustainable Building Material
As society becomes more conscious of the environment and the impact of human activities on it, the construction industry has begun to embrace sustainable practices. One of the most promising materials for sustainable architecture is hemp. Hemp is a versatile crop that has been used for centuries for various purposes, from textiles to medicine. In recent years, researchers and architects have rediscovered its potential as a building material. Hemp-based materials offer numerous advantages, including durability, energy efficiency, and low carbon footprint.
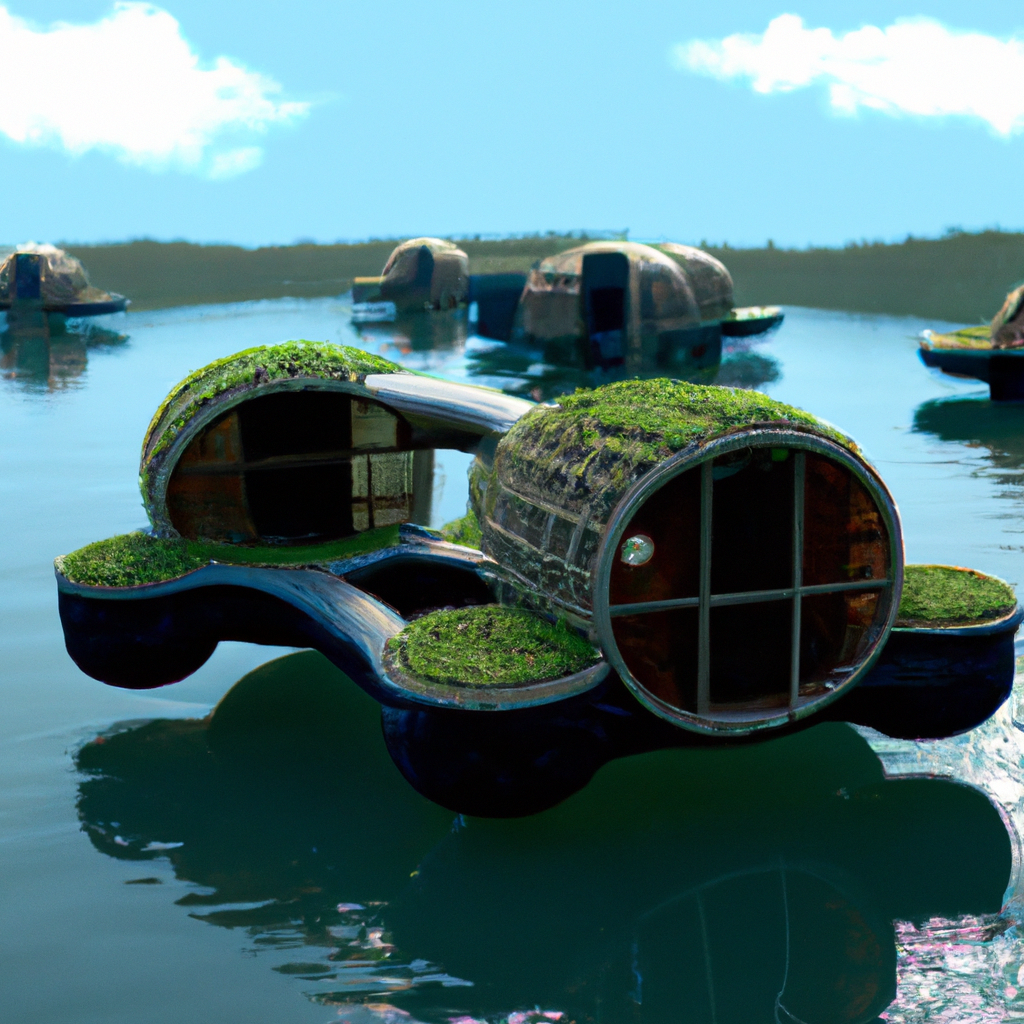
Hempcrete: A Durable and Efficient Insulator
Hempcrete is a bio-composite material made from hemp hurds, lime, and water. It’s an excellent insulation material that can improve the energy efficiency of buildings. Hempcrete is porous, which allows it to regulate moisture and humidity levels in a building. This feature makes it ideal for regions with extreme weather conditions. Additionally, hempcrete is fire-resistant, lightweight, and has a low carbon footprint.
One of the main benefits of hempcrete is that it’s durable. Buildings made from hempcrete have been known to withstand earthquakes and natural disasters. Hempcrete structures have also shown to have excellent acoustic properties, which makes them suitable for sound insulation. Hempcrete is still a relatively new material, but it shows great potential for revolutionizing the construction industry.
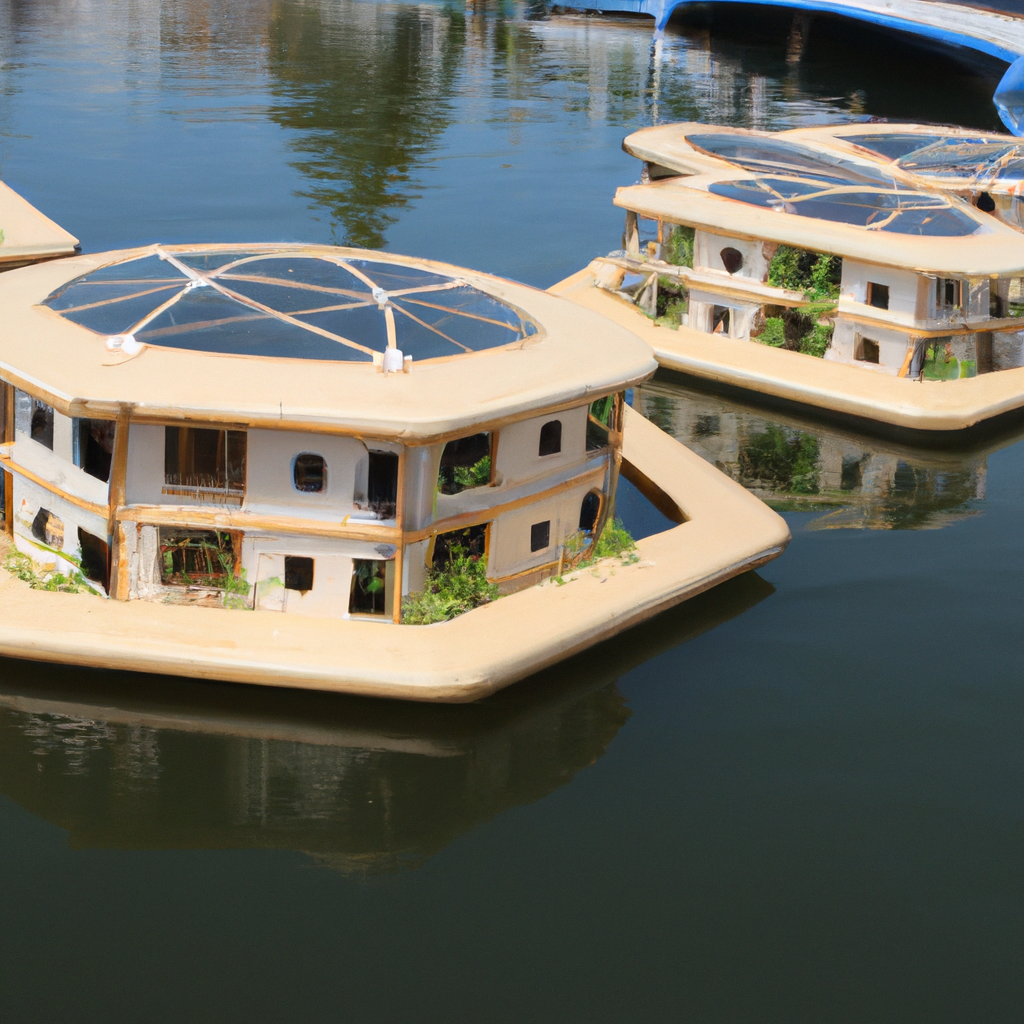
Hemp Fiber: Strong and Versatile for Structural Use
Hemp fibers have been used for centuries for textiles, ropes, and paper. However, recent research has shown that hemp fibers can also be used for structural purposes. Hemp fibers are strong, lightweight, and have a low elasticity coefficient. These properties make them an excellent alternative to traditional building materials such as steel and concrete.
Hemp fibers can be used to reinforce concrete, which improves its strength and durability. Hemp fibers can also be used to create composite panels, which can be used for flooring, roofing, and walls. A hemp-based composite panel is a sustainable alternative to traditional wood-based panels, which are often made from non-renewable resources.
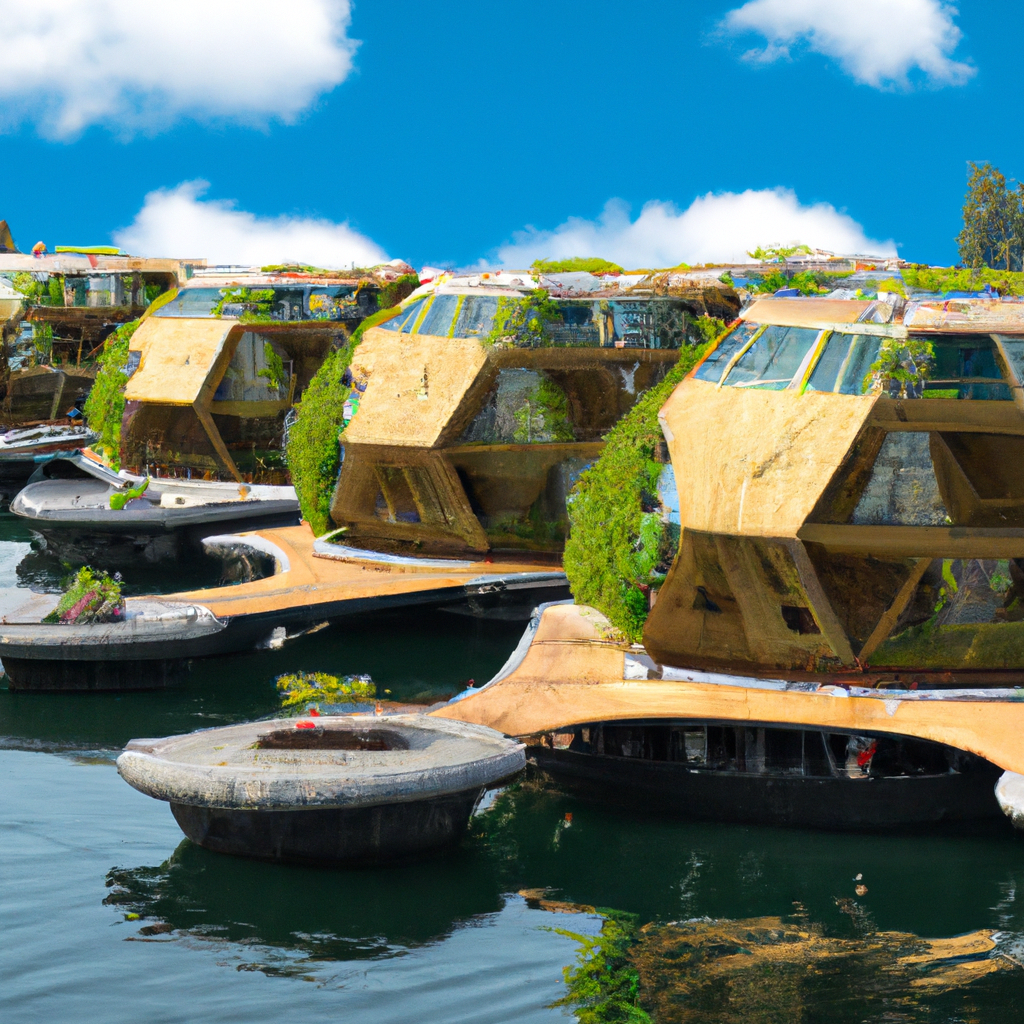
Environmental Benefits of Hemp in Architecture
The environmental benefits of hemp-based architecture are numerous. For starters, hemp is a fast-growing crop that requires minimal water and fertilizers. Hemp plants also absorb carbon dioxide from the air, which makes them an excellent carbon sink. Hemp-based materials also have a low carbon footprint because they require minimal energy to manufacture.
Another environmental benefit of hemp-based architecture is its potential to reduce waste. Hempcrete, for example, can be recycled and used as a soil conditioner. Additionally, hemp fibers can be composted or used as animal feed. By using hemp-based materials, architects and builders can contribute to a more sustainable and circular economy.
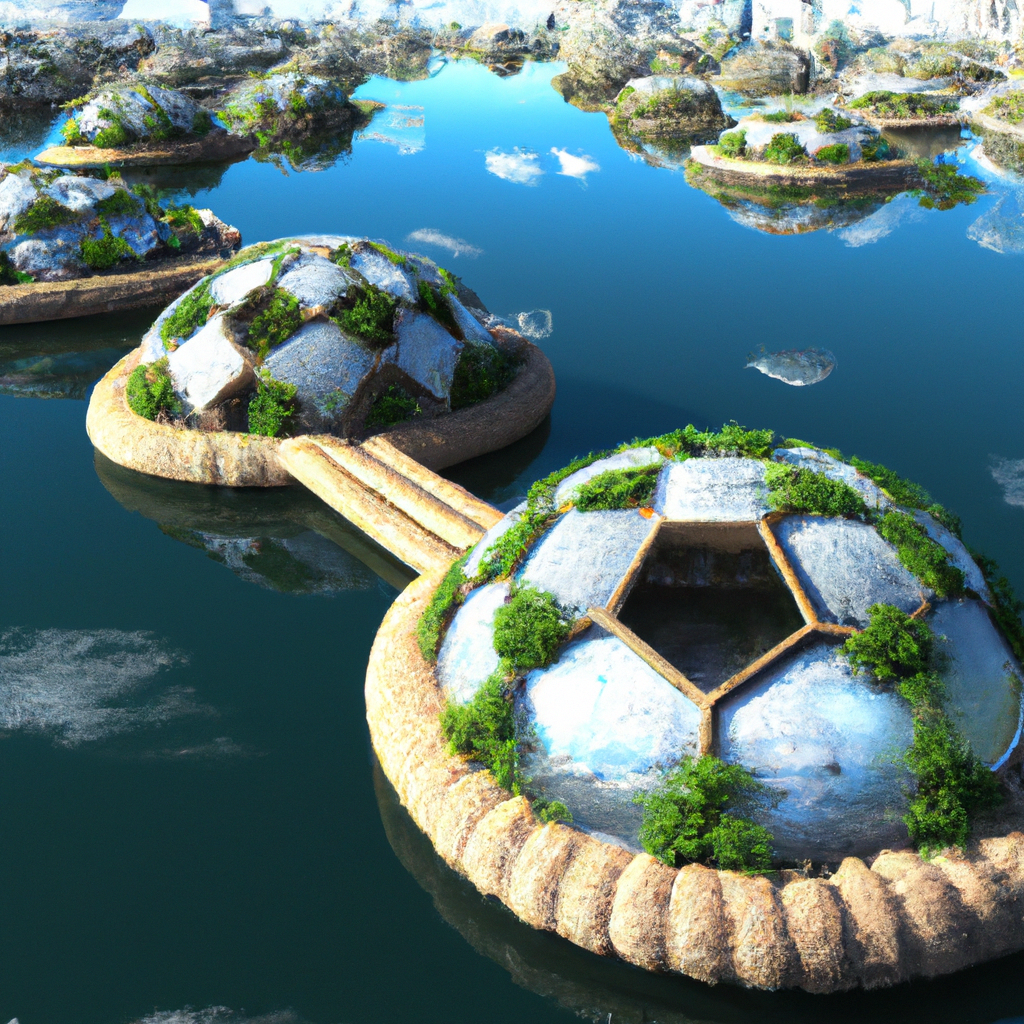
Hemp-Based Materials for Interior Design
Hemp-based materials are not only suitable for exterior construction but also for interior design. Hemp fabrics and textiles have a soft texture and can be used for upholstery, curtains, and bedding. Hemp fibers can also be used to create decorative panels, which can be used for walls and ceilings. Hemp-based materials offer a natural and aesthetic appeal that can enhance the ambiance of a space.
Overcoming Regulatory Challenges for Hemp-Based Architecture
Despite its potential, hemp-based architecture faces regulatory challenges. In many countries, hemp is still classified as a controlled substance, which limits its use in construction. Additionally, building codes and standards often require traditional materials, which can discourage architects and builders from using hemp-based materials.
To overcome these challenges, there is a need for regulatory reform and public education. Governments must recognize the potential of hemp-based materials and develop policies that promote their use. Additionally, architects and builders must educate themselves and their clients about the benefits of sustainable architecture and the potential of hemp-based materials.
In conclusion, hemp-based architecture represents a promising opportunity for sustainable construction. Hemp-based materials offer numerous advantages, including durability, energy efficiency, and low carbon footprint. With proper regulation and public education, hemp-based architecture can contribute to a more sustainable and circular economy. As we strive towards a greener future, hemp presents an exciting prospect for the construction industry.